Different plastic materials have other molding processes, including injection molding, extrusion molding, suction molding, blow molding, calendering molding, foaming molding, plastic lining, dip molding, and so on.
The following introduces the working principle and suitable plastic material of these forming methods.
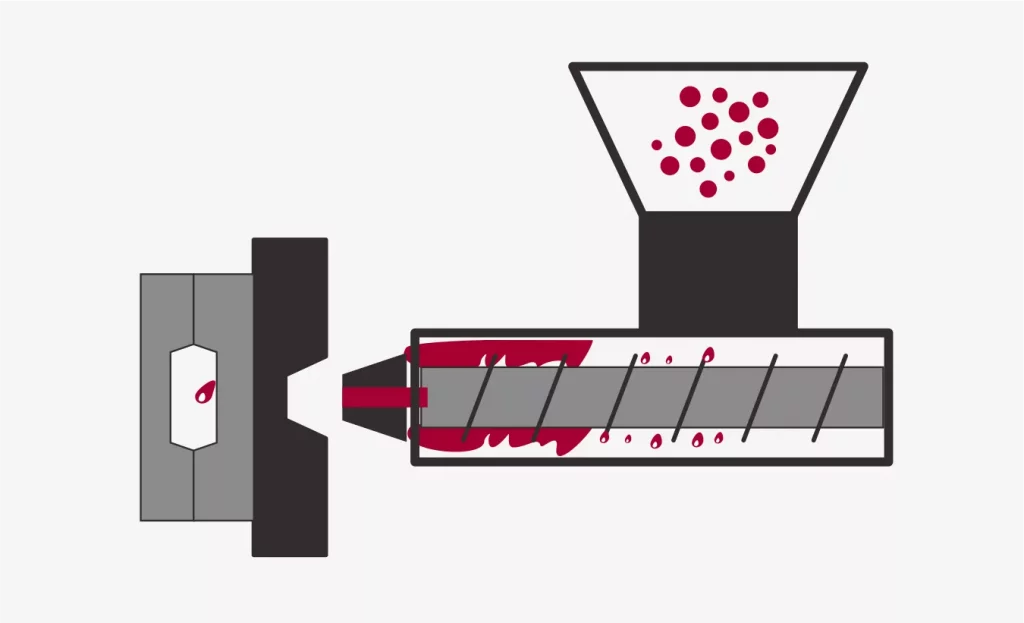
1. Injection Molding
It is an injection molding method. With the development of the economy, people have higher requirements for product quality in industrial production. Injection molding is the most widely used plastic molding method because the industry is the most precise and can produce higher precision products.
Injection molding is at a certain temperature, through the screw stirring, completely melted plastic material, with high pressure shot into the mold cavity, the method of forming products after cooling and curing.
- The following are injection molding processes:
① Mold closing,
② Injection plastic,
③ Pressure holding,
④ Cooling,
⑤ Mold opening,
⑥ Take out the products
The above process repeated, can batch periodic production of products. Thermosetting plastic and rubber molding also include the same process. Still, the barrel temperature is lower than thermoplastic plastic, the injection pressure is higher, the mold is heated, the material injection completed in the mold needs to be cured or vulcanized process, and then hot de film.
2. Extrusion molding
Extrusion molding is in non-rubber extrusion machine processing using hydraulic pressure in the mold itself extrusion weighing pressure. It is heat plasticized, the side is pushed forward by the screw, continuous through the head, and made into various cross-section products or semi-products of a processing method.
Thermoplastic or thermosetting molds are loaded into the hopper and barrel. They are heated, plasticized, and pushed forward by screw placement through a nozzle with the desired section.
Extrusion is a continuous, low cost, high efficiency, adaptation of wide processing methods, the occurrence of early in polymer materials processing is a technology, after 100 years of development, extrusion molding is in the field of polymer processing production of most varieties, most change, high productivity and strong adaptability, a wide range of USES, production accounted for the largest processing method. Extrusion molding is one of the most important forms of plastic material processing, and it is suitable for most plastic materials except some thermosetting plastics.
3. Absorb plastic molding
Absorb plastic molding is also called hot forming. When forming, the thermoplastic sheet or sheet is clamped up and fixed on the mold, heated by the radiation heater. When heated to the softening temperature, the air between the sheet and the mold is pumped by a vacuum pump. Under the action of atmospheric pressure, the sheet is stretched and deformed to the surface of the mold, and the product is shaped after cooling.
Absorb plastic molding can form packaging products, such as drug packaging, disposable meal boxes, and electronic products, such as button battery packaging. The thicker plate can also form shell cover products such as refrigerator liners, bathroom mirror boxes, etc.
4. Blow molding
Blow molding is a rapidly developing plastic processing method. During World War II, the blow molding process began to produce low-density polyethylene vials. In the late 1950s, with the birth of high-density polyethylene and the development of blow molding machines, blow molding technology was widely used. The volume of hollow vessels can reach thousands of liters, and some production has been computerized. Suitable for blow molding plastic polyethylene, polyvinyl chloride, polypropylene, polyester, etc., the resulting empty container is widely used as an industrial packaging container. According to the method of making billet, blow molding can be divided into extrusion blow molding and injection blow molding, the new development of multi-layer blow molding, and stretch blow molding.
The heated thermoplastic extrusion tube is placed between the two halves of the open die, and the gas pressure is applied to make it expand against the closed die sidewall, open the die, and push out the product. Blow molding is often used in daily industry to form car fuel tanks, warm air channels, chemical packaging containers, portable tool cases, etc.
5. Calendaring molding
Calendering is a processing method that makes the viscous material be extruded and extended many times by means of the strong shear force between rollers and the corresponding processing temperature. Finally, it becomes the thin section products with width and thickness. Plastic and rubber are calendering molding processes, plastic with PVC resin as the main raw material.
The doughy thermoplastic melt is made into a plate of uniform thickness by tandem heating or cooling roller rolling. It can also be used to press plastic mulch onto the back of other materials.
Calendering is a forming method for producing polymer films and sheets used for plastics and rubber. Composite products can be made by simultaneously treating paper or fabric between the last pair of rollers. The hot plastic or rubber film is bonded only under roller pressure to these substrates. This method is called calendering or, for rubber, pasting. The artificial leather that everybody is familiar with, floor change, and wallpaper are all plastic and base material compound goods.
6. Foam forming
It is the general term for making foam plastic forming method. According to the classification of foam manufacturing methods, it can be divided into two categories: the method of foaming plastic raw materials with a process is called one-step foaming method, also known as the direct method, polyurethane foam is its typical representative; The method of making foam plastic by two processes is called two-step foaming method, also known as an intermittent method.
In the foaming process or foaming polymer material, the cellular or porous structure is formed by the addition and reaction of physical or chemical foaming agents. The basic steps of foaming are the formation, growth, or enlargement of the nucleus and its stabilization.
At a given temperature and pressure, the solubility of the gas decreases so that it reaches a saturation state, allowing the excess gas to be expelled and form bubbles, thus achieving nucleation. Almost all thermosetting and thermoplastics can produce microporous structures made into foam plastics. Commonly used resins are polystyrene, polyurethane, polyvinyl chloride, polyethylene, urea-formaldehyde, phenolic, etc.
7. Vinyl molding
Vinyl is a kind of technology to do toys. With this approach to make the material a little soft, have a very good elasticity, generally used to do dolls, generally hollow, but also solid, the cost will be high.
Since 1924 Germany was born the first keep out glue machine on the world, make the first toy successfully “chocolate rabbit” that day rise, keep out glue distinctive model force is destined to bring endless vision new experience for this world. Glue adds colorful colors for traditional entertainment with the popularity and popularity of a series of representative works.
Keep out the glue product material is special. PVC coarse powder and PVC young powder also need to add plasticizer, hard oil, and other components, resulting in the final product and ordinary PVC toys touching the hand board being different.
Probably because of that, leading to many people feeling that the glue is a kind of material the adhesive is a kind of manufacturing process, in this popularity.
Categories
Share On
Recent Post
Self-tapping Screws Of Plastic Injection Molding Parts
In the development and design stage of new products, the
Injection Molding Screw Post Design Guide
The screw is one of the most commonly used locking