Have you ever wondered how to make injection molds? You may be surprised to learn that this process is easier than you might think! There are a few basic steps that need to be followed in order to make injection molds. In this blog post, we’ll explore all of the steps involved, from the initial design to testing. Injection molding is a common practice, but it can be intimidating to someone who has never done it before. This blog post will serve as a complete guide to making injection molds.
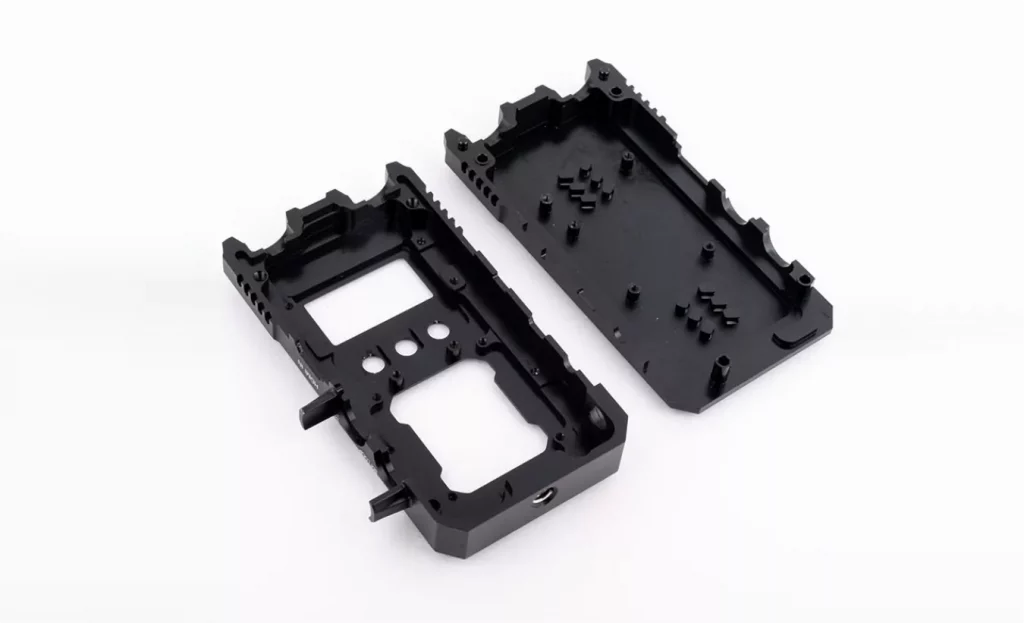
1. Factors to be Considered While Making Injection Molds
There are a few factors that you need to take into account while making injection molds. The first is the material you will be using to make the mold. You need to make sure that the material can withstand the heat and pressure that will be exerted on it when the plastic is injected. The other important factor is the design of the mold. You need to make sure that the mold can be easily split apart so that you can remove the product once it is cooled. Finally, you need to make sure that the mold is robust enough to withstand the pressure of the plastic being injected into it.
2. The Phases of Making Injection Molds
# Mold Design Importance To Make Injection Molds
The design of the mold is extremely important in the manufacturing process of injection molded parts. In fact, the mold is the most expensive component of the whole process. The mold needs to be designed with the parting line, runners, and gates in mind. If these are not designed properly, the part will not come out correctly and the mold will need to be scrapped. Injection molding is a process where molten plastic is injected into a mold cavity. The molten plastic then cools and hardens to form the part.
# The process of Injection Mold Making
Injection mold making is a process that starts with a 3D model of the part you want to create. This 3D model is then used to create a mold, or the “negative” of the desired part. The mold is then used to create a “positive” of the part, which can be used to create the final product. The final product is created by injecting molten plastic into the mold and allowing it to cool. This process is used to create products such as cups, eyeglasses, and car parts.
# Injection Mold Testing
After your injection mold is created, the next step is testing it. This is an important part of the process, as it ensures that your mold is functioning properly and meets all of your expectations. There are a few different ways to test your mold, and the method you choose will depend on your specific needs and requirements. One popular option is to use a pressure test. This involves filling the mold with a liquid and measuring the amount of pressure needed to produce a fracture in the part. This can help you determine the maximum loading capacity of your mold. You can also test the fit of your mold by using a prototype part. If everything looks good, you’re ready to start producing parts!
3. Benefits of Making Injection Molds on Your Own and on a Large Scale
There are several benefits to making injection molds on your own. First, it’s cost-effective. You can make as many molds as you need without spending a fortune. Second, it’s a great way to produce large quantities of products quickly and easily. And finally, it’s a great way to customize your products exactly the way you want them. You can control the shape, size, and design of each and every mold. You’re limited only by your own imagination!
4. How to Make Injection Molds in an Industry
Injection molding is a process used to create high-quality, durable products from a variety of materials. It’s commonly used in the manufacturing industry to create products like automotive parts, medical devices, and household appliances. Injection molding is a complex process, but with the right tools and knowledge, you can create your own injection molds at home. Continue reading and this guide will walk you through the entire process, from finding the right materials to assembling the mold. Let’s get started!
5. DIY Injection Molding Short Process
So you’ve decided you want to start making injection molded parts? Great! This tutorial will take you through the entire process, from start to finish. We’ll cover everything from designing your part to making the mold to injection molding the part. Injection molding is a great way to quickly and cheaply produce high-quality parts in large quantities. With the right tools and some patience, you can start making your own injection molded parts today.
# Design the Mold in CAD
The design of the mold is one of the most important steps in the process. This is the step where you have to decide what the part will look like, how it will be made and what features it will have. Injection molding is a complex process, and the mold is a major part of that. The mold needs to be able to withstand the high pressure and heat of the injection process, as well as the repeated use. That’s why it’s important to get the design of the mold right the first time. CAD software can help you create a perfect 3D model of your part that you can use to create the mold.
# 3D Print the Mold
The final step is to print the mold using a 3D printer. This will create the final, actual-sized mold. If you’re not sure how to go about this, there are plenty of online tutorials to help you out. You can also find 3D printing services that will do the job for you. Printing the mold is a crucial step, as it will ensure the finished product is of the highest quality.
# Injection Molding the Plastic Parts
The fourth step is injection molding the plastic parts. This step is where the molten plastic is injected into the mold cavity. The plastic is then allowed to cool and solidify. The part is then ejected from the mold and the process starts over again. Injection molding is a very fast and efficient process, and it can produce high volumes of parts in a short amount of time.
Categories
Share On
Recent Post
Self-tapping Screws Of Plastic Injection Molding Parts
In the development and design stage of new products, the
Injection Molding Screw Post Design Guide
The screw is one of the most commonly used locking