Our Capabilities
A wide range variety of manufacturing capabilities offer a turnkey solution that bring your projects to completion
1M +
Parts Made
300 +
Customers Served
6000
Qunique Designs
6000
Qunique Designs
Processing Capabilites Of Plastic Parts
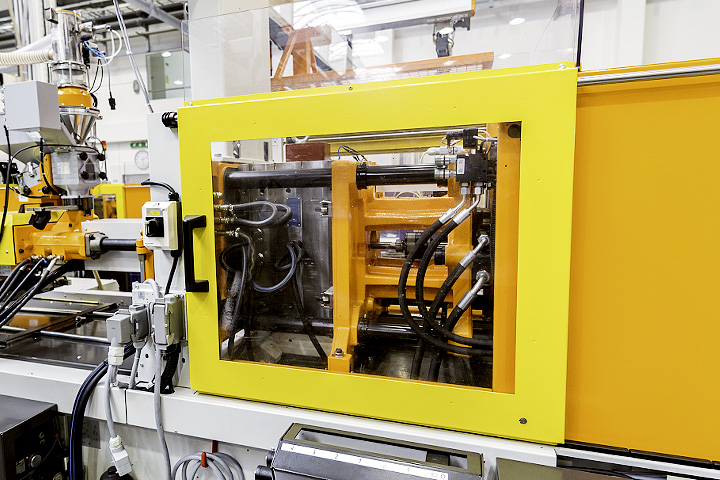
Injection Molding
Our mold making process is based on established methodologies, we can quickly transform design drawings into high-quality parts that are ready to ship within two weeks.
- Design
- Analysis
- Mold production
- Part production
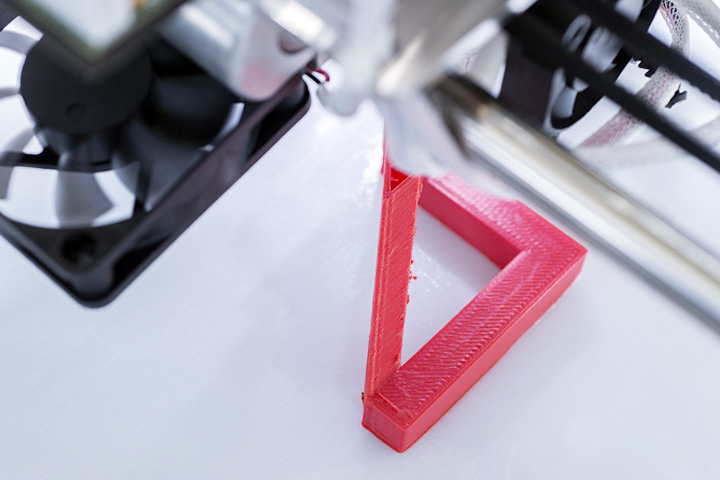
3D Printing
This is a process by which high-precision parts are made by injecting molten metal into custom-made steel. with exceptional surface finish and impressive dimensional accuracy.
- Complex geometries are possible
- Excellent surface finish and accuracy
- Mass production
Suitable for larger metal parts
Processing Capabilites Of Plastic Parts
By combining data from thousands of projects using proven material and molding techniques, our injection optimization process can quickly and easily determine correct machining parameters. These measures allow us to efficiently walk new molds through the testing phase and into production within hours.
We can complete parts quickly and correctly while achieving exceptional materials and parts geometries. We can reduce or even eliminate defection from plastic parts during the injection molding procedure.
Our Injection Molding process optimization does away with quality issues caused by molded-in stressors such as these:
3D Printing Capabilites
We rely on three additive manufacturing processes. These processes are: fused deposition modeling (FDM), stereolithography (SLA) and and selective laser sintering (SLS)
Fused deposition
modeling (FDM)
Fused deposition modeling (FDM) uses extruded melted filament through a nozzle to manufacture parts layer by layer. With a broad range of available materials, FDM works well for prototyping and in end-use production.
Stereolithography
(SLA)
SLA uses light to crosslink monomers and oligomers that form rigid polymers photochemically. This method is suitable for marketing samples, mock-ups and other non-functional conceptual samples.
Selective laser
sintering (SLS)
SLS uses a computer-controlled laser to sinter a powdered material like nylon or polyamide layer by layer. This process produces accurate, high-quality parts that require minimal follow-up or support.
Aria Vs Ohter Injection Molding Companies, What is Difference
Aria's Mold Making Process Offers Highly Competitive Advantages
Some projects require a higher production rate than others. When that happens, we build multi-cavity and automated tooling to offset extra costs with higher productivity rates and lower unit costs. In our end-to-end facility, in-house injection molding production is accom-plished using high-stability aluminum and tool steel.
Common Features of Our Injection Molding Projects
Our computerized numerical control (CNC) system and electrical discharge machining (EDM) equipment produce standard accuracies on a tool of +/- 0.005”. Tighter tolerances are available on demand with a small fee.
Processing Capabilites Of Metal Parts
Pressure Die Casting
This is a process by which high-precision parts are made by injecting molten metal into custom-made steel. with exceptional surface finish and impressive dimensional accuracy.
- Complex geometries are possible
- Massproduction
- Suitable for larger metal parts
- Excellent surface finish & accuracy
Mold Making
Our mold making process is based on established methodologies, we can quickly transform design drawings into high-quality parts that are ready to ship within two weeks.
- Design
- Analysis
- Mold production
- Part production
Sheet Metal
Sheet Metal is a cost-effective solution for metal components with a uniform wall thickness of less than 6mm. Sheet metal is appropriate for high-quality cutting, punching, bending and welding procedures.
- Parts thickness 0.5 – 10mm
- Fastest delivery 3 working days
CNC Machining
This subtractive manufacturing process removes raw materials with various precision cutting tools to create parts, prototypes and finished products.
- Milling, Turning
- Wire EDM
- Surface grinding
- Electrical discharge machining (EDM)
DFM Analysis Support
A design for manufacturing analysis (DFM) is used to determine whether the design of a part is compatible with the desired production method. DFM reports focus on these variables:
Reducing tooling costs
The computerized CNC machine cuts through the metal piece and produces an exact design with minimal waste. they are environment friendly and will save a lot of money and manpower.
Limiting design change costs
We design parts to correspond as closely as possible to the original design. However, modifications may be necessary to meet the fundamental requirements of a process.
Expediting the manufacturing process
An initial analysis will be conducted based on an appropriate 3D design file. Our goal is to ensure that the parts in question are suitable for injection molding, CNC machining, 3D printing and other select procedures.
Guaranteeing quality parts
The CNC milling process uses CNC machines that are not that complicated to assemble. CNC machines are most easy to assemble and use. The manual assembly is straightforward, and even a single person can assemble the entire machine.
Processing Of Materials
CNC Machining
Aluminum
Stainless steel
Mild, Alloy & Tool steel
Other Common Metals
5052
201
Mild steel 1008
Brass 260
5083
303
Mild steel 1018
Brass 2680
6061
304
Mild steel 1020
Brass 360
6061-T6
316
Mild steel 1025
Brass 385
6061-T651
316L
Mild steel 1045(#45)
Brass H59
6063
401
Alloy steel 1215
Brass H62
6082
410
Alloy steel 4041
Bronze
ADC12 (A380)
416
40Cr steel
Copper 101
416L
Alloy steel 4130
Copper 110
420
Alloy steel 4137
Titanium TC2
430
Alloy steel 4140
Titanium TC4
440C
Alloy steel 4040
Titanium TC5
Tool Steel A2
Tool Steel A3
Tool Steel D2 (Mould steel)
Tool Steel S7
Plastic Materials
Commom Plastic
Reinforced Plastic
ABS
Garolite G-10
Polypropylene
Polypropylene (PP) 30%GF
Nylon 6
Nylon 30%GF
Delrin (POM-H)
FR-4
Acetal (POM-C)
PMMA (Acrylic)
PVC
PEEK
HDPE
UHMWPE
Polycarbonate
PET
PTFE (Teflon)
Additional Capabilities
Stamping
Stamping is a fast and efficient solution. Using the press, a tool and die surface shapes the metal into its desired form. Blanking, punching, bending, coining, embossing and flanging are all stamping methods used to shape metal.
Laser marking
Laser marking works well for making permanent markings on the surfaces of metals and certain plastics. The process doesn’t change part geometries or interfere with the mechanical properties of the substrate.
Assembly
Light commercial assembly is available both in-house and from a subcontractor. Because there are so many application possibilities, we suggest that you clarify your needs with an account manager before diving in.
Custom packaging
Custom packaging. Metal joinery is available in the form of welding, soldering and brazing. However, we only outsource these services for select projects.
Engineering Support
Our experienced engineering team is always ready to offer assistance. You will receive professional suggestions from early-stage model selection to money-saving tips and technical reminders before manufacturing. This includes custom prototype design advice.
After-Sales Service
At Aria, quality is our top concern. We deliver SGS, or RoHS metal certification, and 4D reports.
Upon request, our “Parts Verification Process” is available. For added protection, we have a generous return and refund policy.
Get A Free Quote For Your Project Today
All information and uploads are secure and confidential.
Frequently Asked Questions
CNC machining is a wide-ranging manufacturing category involving multiple computer-managed processes. The objective is to remove enough raw material from a piece to achieve a state of near completion.
Aria is a professional CNC machining manufacturer in China, The reliability and precision of high-tech tools powered by sophisticated software programs give CNC machining the ability to quickly generate prototypes and complicated end-use parts having exceptionally tight tolerances. with low cnc machining costs from Chinese.
CNC machining is a subtractive manufacturing process. When the material is added instead of removed, it’s called an additive manufacturing process. Examples of subtractive CNC machining include specialized applications such as CNC milling services, turning, surface grinding, and EDM. An example of additive CNC machining is 3D printing.
Computer-aided design (CAD) files are digital records containing 3D designs and information about materials, processes, tolerances, and other variables. A digitally controlled CNC machine must always contain a file of the part design that controls it.
The spinning motion from the CNC machine’s cutter will leave visible tool marks. Although they stand ready for immediate service, they can be further refined with anodizing, painting, polishing, and plating.